Our repair ethos meets the demands of the hire industry:
We see Jayville Engineering products in for repair rarely. However, we support our hire company customers with a repair service for other manufacturers’ products from drag boxes to hydraulic braces. We focus on what needs doing to make sure the product passes British and European standards and is back in use quickly.
A Jayville repair commences with a damage assessment and a Repair Approach Report (RAR). This details how the repair will be made and any updates required. It illustrates whether a repair is economical in comparison to replacement and seeks authorisation for the work. This keeps you in control.
All work is carried out by our experienced repair team. They are specialists from code welders to skilled engineers. Repairs are made to high standards and assessed before being finished with robust paints. We can repaint the product to match branding requirements or simply paint the repaired area blending this into the original colour. Our finishing enhances product durability in the field.
We repair all trench shoring products, so let us help get your damaged equipment back to good working order and making money for you.
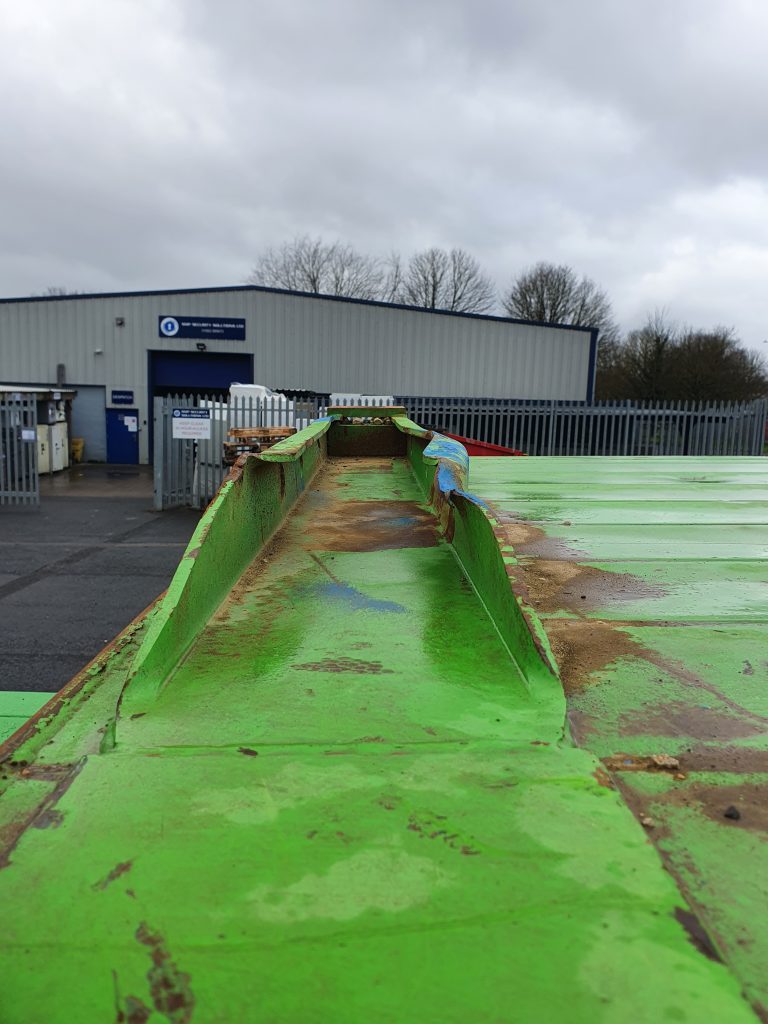
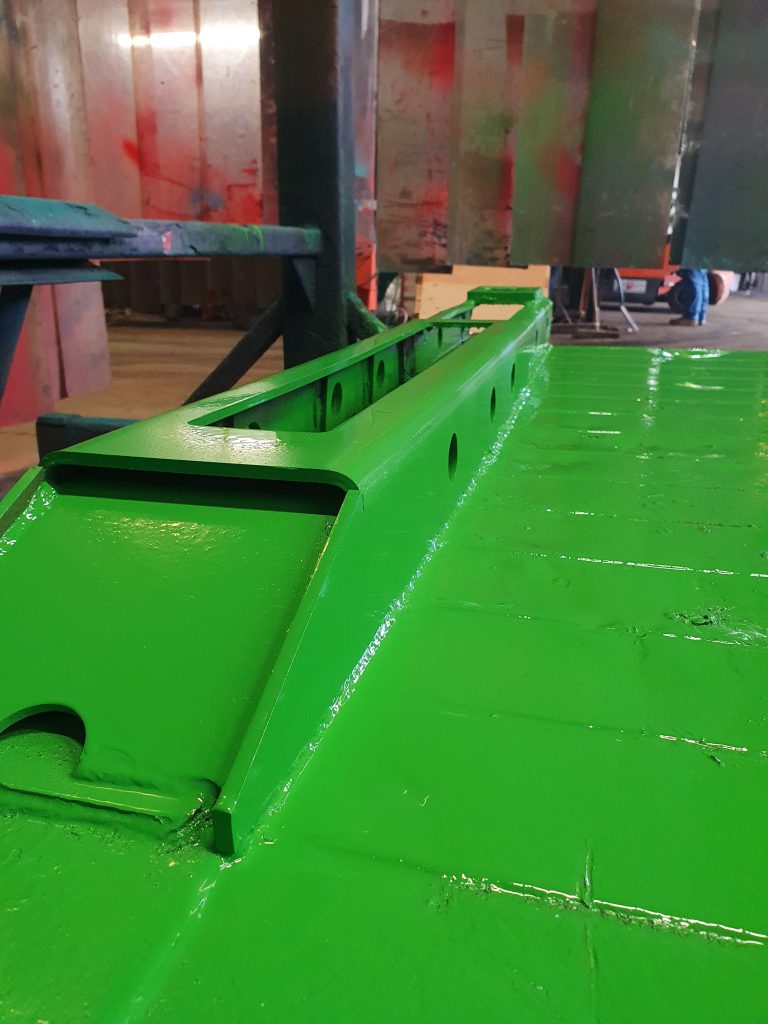
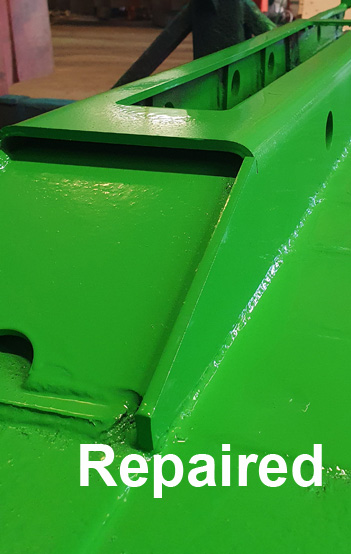
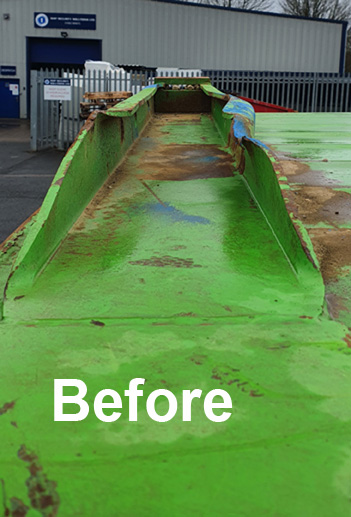
Drag left or right to see the full image
No hire company likes a repair. They cost money in materials and reduced rental time. Importantly, our repair ethos meets the demands of the hire industry:
A rapid, economic, fit for purpose repair to maximise rental revenue
Simply put, we will help you get unusable equipment back out into the field again quickly. British shoring techniques are different from those used across Europe increasing the number of times products are installed and removed during a build product. Over time, many manufacturers’ products suffer significant wear and tear during multiple dig and push or dig and place installations. We repair a wide range of products that don’t have the durability and resilience of the Jayville range.